Used oil plantsUsed oils from all industrial sectors are transformed in these plants. Product quality - heating oil or diesel - is mainly determined by the substances used. Many used oils were optimised by additives for their original application and thus have a high sulphur level. This sulphur can sometimes still be found in the product. Depending on the incoming substances, the plant operator has the possibility of leaving the residual sulphur share in the product following depolymerization and selling it as heating oil or of setting up a desulphurisation plant downstream in order to be able to use the product for operating diesel aggregates of all kinds.
The current system size is 4000 to/a. By modular arrangement, units of up to 40.000 to/a can be set up. The recycling process begins with the acceptance of used oil at the plant. The used oil is pumped from a tanker into a supply tank. From there it is fed into the reactor of the depolymerization plant via an intermediate tank once it has passed through a fine filter.
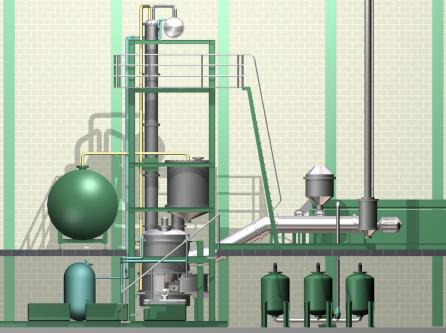
Before this, the oil is heated recuperatively to approx. 150 degrees to remove water and other easily combustible materials. Following the depolymerization process, between 3% and 5% residual materials are left over - depending on the purity of the incoming substances.
Current concepts plan to use these bituminous materials for road building since they do not contain any serious pollutants.
The operator gains double benefit. He receives payment both for accepting used oil for disposal and for the sale of the process product.

Polymer plantsIndustry and households continually produce large quantities of plastic waste. These are often soiled to a differing degree. The respective degree of soiling has a major influence on plant efficiency. Efficiency has been determined using test batches, thus establishing the key data required for calculating the economic feasibility of incoming substances. Whether the incoming substances contain PVC or other substances containing chlorine is also very important. In this case a special additive is added to the reactor chamber which transforms the chlorine into common salt (NaCl) which remains in the residual materials disposed of from the reactor.
Plastics can be delivered in pellet form, as pressed bales or loose. Depending on the condition on delivery, the materials must be pre-treated in a suitable way before they are fed into the depolymerization plant.
Here, a preheating to approx. 250°C takes place, water is vaporized by friction and the plastic is injected into a reactor, where it is decomposed and depolymerized.
In this case, the system size of 4000 to/a up with the possibility of modular arrangement can also be selected. In this case as well, bituminous substances remain as residuals, provided that the limit values for heavy metal content are adhered to.
The acceptance of plastic waste is currently an extremely lucrative business, whereby it depends on the degree of purity and form of delivery, of course.

Flushing oil plantsFlushing oils are residual products from cleaning oil tanks. Here, sludge residue from oil tanks is dissolved in special flushing oils.
Due to their similarity to used oils, this transformation process is very straightforward and closely linked to used oil depolymerization. The filtered flushing oil is fed into the reactor as described above and depolymerised.
Secondary waste is produced according to the amount of soiling in the flushing oil. Method and workflow correspond to used oil recycling details.

|